The Strategy
Simulating Reality
The vision of ESI Group, since its creation in 1973, is to solve real and practical engineering problems of several industries. These simulation solutions, based on the physics of materials, achieved a world-premiere in 1985: for the first time, a virtual crash test was performed for Volkswagen, paved the way to the massive adoption of virtual solutions in engineering processes and established new safety standards.
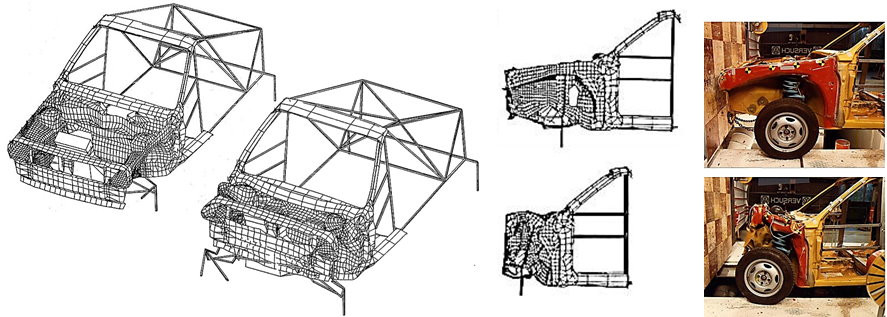
A new paradigm, the Outcome Economy
Increasing complexities are challenging all industries. Manufacturers are facing many challenges to satisfy the customer’s needs in terms of quality, reliability, safety, and on-time delivery. The Outcome Economy made the Key Performance Indicators more difficult to meet, as success is measured by performance rather than the product itself. Industries need to achieve growth while maintaining innovation. Therefore, they opt for a digital transformation that might lead them to initatives with no demonstrated results.
Transformation Journey
The Group’s offered solutions, resulting from 45 years of experience, bring technological empowerment to innovate efficiently and with confidence.
Paramount of ESI’s business model, Virtual Prototyping allows its global customers to validate the manufacturing, assembling, and behavior of their product in different environment minimizing their costs and time to market, without sacrificing safety and quality. To reach these objectives, ESI accompanies its customers in a journey towards Zero Tests, Zero Prototypes and Zero Downtime.
ESI strived to provide the best answer for the industries’ problems and to keep its promises to boost agility and push innovation. Confining the physics of material in its DNA, ESI supports industries to validate the fabrication, assembly, and behavior of the product in different environments – early and throughout the whole product life.
Make the difference with Virtual Prototyping
The ability to experiment virtually with real data and real physics at the same time gives engineers just the extra degree of freedom they need to design right the first time.
- It is the freedom to displace physical tests and prototypes by virtually replicating product development, testing, and manufacturing with simulations. At ESI, we call this Virtual Prototyping. A Virtual Prototype is based on multi-domain simulation models and captures ESI’s unique treasure of material physics. Supplemented by advanced Virtual Reality, engineers experience in full immersion their latest designs prior to production. Our customers rely on Virtual Prototypes to digitally demonstrate reliability, safety, and energy efficiency upfront in the development cycle and to pre-certify their new technology right the first time.
- It is the freedom to assess the ageing and behavior of a product at any stage and in any situation during its life. This is what the industry commonly refers to as Digital Twin. At ESI, we went the extra mile in creating a new virtual paradigm. Equipped with smart sensor data collected from real life operations, our Virtual Prototype becomes artificially intelligent to predict maintenance needs based on its current condition. We call this a Hybrid Twin™. Our customers use the Hybrid Twin™ to ensure a predictive assessment and performance of their products in any operating environment and to improve next generation machines.
It’s All About Performance
Virtual Prototype and Hybrid Twin™ – what do the two have in common? It’s all about performance.
- Towards Zero tests | The performance of design and development for early confidence in the right manufacturing and assembly process without the need for real tests.
- Towards Zero prototypes | The proof of performance in terms of safety and sustainability without the need for real pre-production prototypes.
- Towards Zero downtime | The performance of the final product in terms of reliability with zero downtime during operations.
Performance is the game-changer for our customers’ future business models. Therefore we, at ESI, are evolving PLM (Product Lifecycle Management) into PPL (Product Performance Lifecycle™). We are convinced that the Management of the PPL is the gateway to get it right®. Our customer stories are proven confirmation.